This is a hot topic on many Facebook groups and forums, where people quickly suggests links and details of what they bought and how good it works.
But very few of these people actually know why it works good, and if it will work good for the reader.
To start off this article – you do not need a big fan to have a good exhaust.
What a big fan does is complementing the problems with the machine and exhaust setup, but you get a hefty electricity bill and loud noise every time you use the machine.
This method is helping your exhaust setup in two ways.
1: Your exhaust fan does not need to put the case in (as much) negative pressure
2: The extra flow will also help with fumes and smoke inside the machine
I dubbed the term “smoke assist” a while back when planning this setup, it´s different from the air assist and focuses on the smoke and exhaust.
Seal your machine
Sealing your case is also a good fix. This will lower the escaping smoke from the machine and reduce the smell to almost zero.
You can do this by adding aluminium tape, silicone sealant or hot glue in each corner and opening on the machine. Add some window rubber seal for the lid to have it air tight when closed.
Moving the exhaust fan
As explained earlier, the exhaust fan in the original configuration has to do a lot of work.
Work it should not have to do.
The fan has to…
1: Put the case in negative pressure and suck air in to the case.
2: It has to suck the smoke past the impeller
3: It has to push the smoke trough the hose out the window.
This is the big reason why some users buy big fans as they were to start a hot air balloon business, the fan has to do a lot of work.
The exhaust should not do this, and almost all fans on the market sucks good, but are very bad on creating a static pressure (pushing air in front of the impeller).
By moving the exhaust fan to the end of the hose, or at least as close you can get will help tremendously with the efficiency of your fan.
How does it work?
Air always want to equalize in pressure, if you have a window open inside your house you can feel the draft from the air equalizing when opening a door. This effect is something we take advantage of in our laser machines and keeping the need for a big fan far away. Chinese sellers want to keep the cost down and price up, they are not engineers and just add the parts that “almost” works. The original exhaust is utterly crap and should be one of the first products you buy.How to optimize your exhaust system
Think of the laser machine as a box, you want a wave of air going trough it with the smallest interference possible. To make this possible you need to add fans to your machine as a intake. It does not matter if you use the front of the machine, or use the bottom/floor as intake.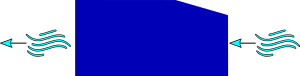
I simple drilled four holes under the bed of my machine, to place the fan. It gives me a great flow of air through the machine, with the air coming through the normal outlet.
I know, that you can’t place the machine on an table, but I think it workshop fine for me.
how do u connect the power to the fans?
It´s always best to have a little extra power plug for any additional stuff you add to the machine. A small 12v 1A wall-wart is enough for some fans.
Hi, what do you think the L/h capacity of the fan should be when placed at the end of the exhaust traject?
It depends, if you seal the machine and put the fan at the end of the hose, you do not need much flow to evacuate the fumes.
I´m using a 200m3/h fan (about 110ft3/min) when cutting acrylic and i do not have any smell at all inside. For cutting wood there is a denser smoke you might want to go up a bit, a fan at 200-250ft3/min would do it, if all suggestions above is solved.
Only by moving the fan to the end of the hose instead of behind the machine increases the efficiency greatly!
Wow 250 cfm is just about 400 m2/h. That’s quite a big (and expensive) fan.
Sorry, was supposed to write 200-250m3/h 😛
It might work with a small one like i have, it´s exactly 187m3/h on full speed, but i never tried cutting wood with my machine. For engraving a smaller one is enough.
Which parts/holes do you exactly seal? In my K40 there’s a hole in the bottom, one to the electrics compartment, two ventilation grids at the front side and obviously the hole to the laser tube compartment. Is it advisable to close all ov these?